


The proposed H-bridge inverter circuit having 4 n channel mosfets tries to overcome this problem by introducing a higher voltage bootstrapping network for operating the high side mosfets. Using 4 N-Channel Mosfets for the Inverter Meaning if the supply voltage is 12V, we would require at least 18-20V at the gate of the high side mosfets.
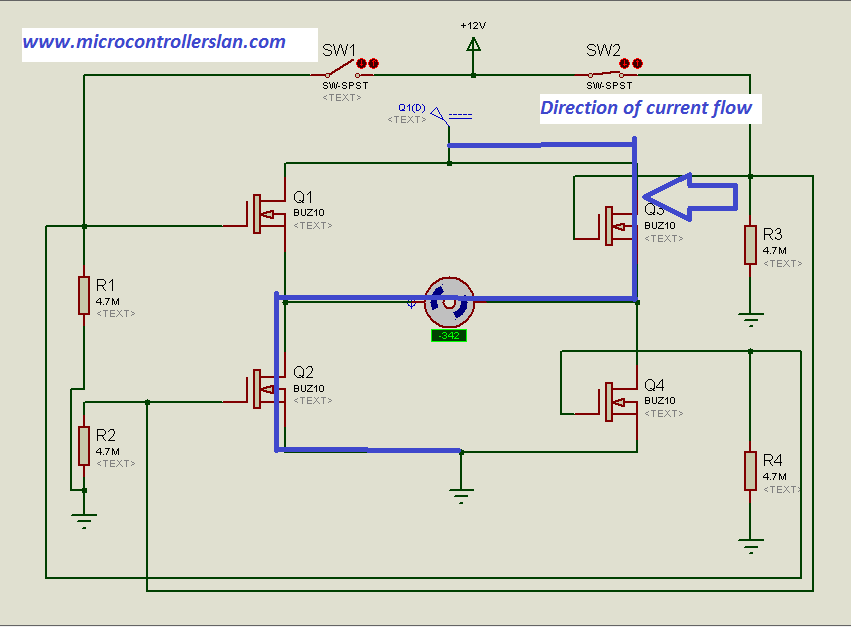
In order to switch the upper mosfets efficiently they must be applied with a gate voltage at least 6V higher than the available supply voltage. Since as per the specs, the source voltage must be close to the ground potential for efficient conduction, the situation instantly inhibits the particular mosfet from conducting, and the entire circuit stalls. That means the upper mosfets come across similar voltage levels at their gate and source while operating. This is because during conduction the upper mosfets experience almost the same level of potential at their source terminal as the supply voltage, due to the presence of the load resistance at the source terminal. With all four of them being N-channel types, driving the upper mosfets or the high side mosfets becomes an issue. It is primarily due to the following facts:Īs we know an H-bridge topology incorporates four mosfets for the specified operations. When identical type mosfets are involved in an H-bridge network, driving them efficiently becomes a big problem. However better things are never easy to get or implement. This provides better efficiency as the attainable current gain here becomes higher than the ordinary center tap type topologies. With a two wire transformer connected to an H-bridge means the associated winding is allowed to go through the push pull oscillations in a reverse forward manner. The results become even better when four N-channel mosfets are involved. We all know that among the different inverter typologies, the H-bridge is the most efficient one, since it does not necessitate the use of center tap transformers, and allows the use of transformers with two wires.
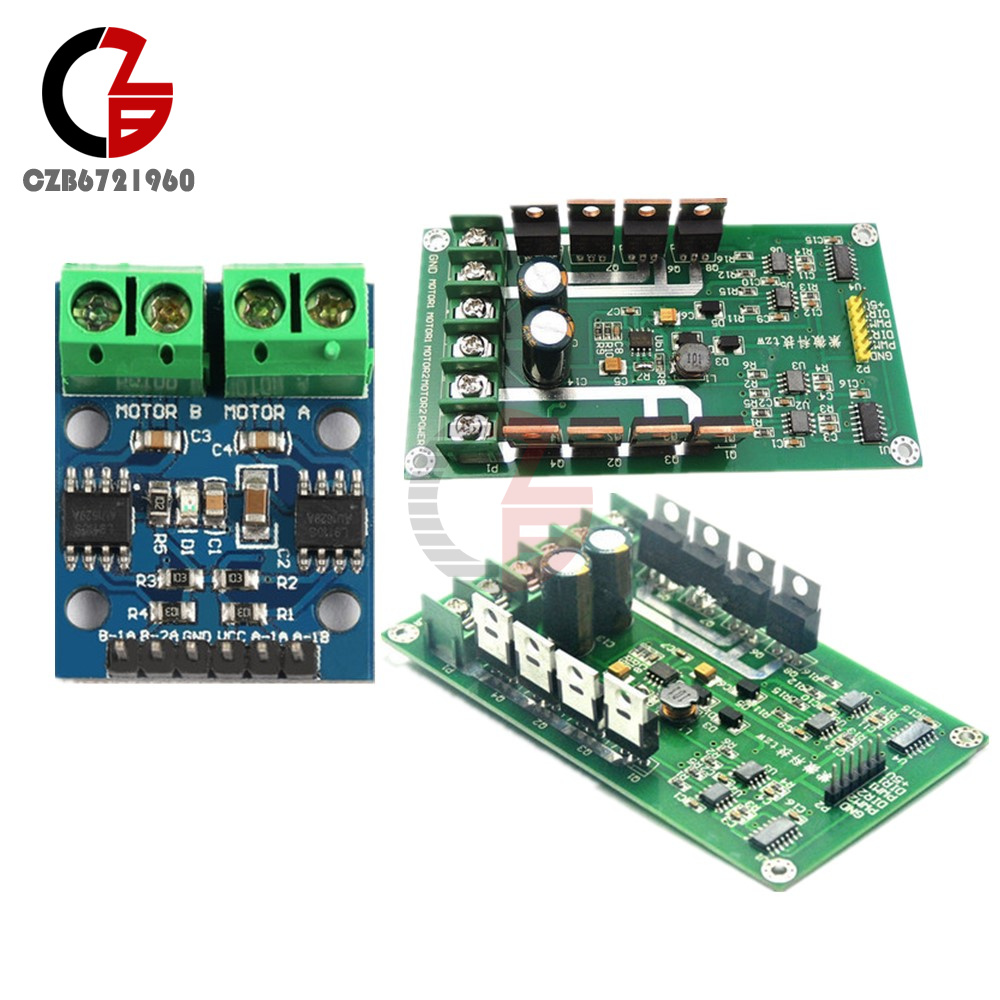
